Evacuating through Schrader valves costs you time, but how much time? We looked at Schrader valves and how they impact evacuation times and what that means for your facility. We set up a simple experiment comparing evacuation:
- Through a Schrader valve
- By a Schrader valve with the core removed
- Via our recommended solution: a process tube with a Hanson quick-connect fitting installed
Evacuating through Schrader Valves: The Results
The video above shows that evacuation through a Schrader valve took about four minutes to reach 300 microns. By just removing the Schrader valve core, we cut the time by about 25 percent (approximately three minutes). But when using a process tube with the Hanson quick-connect fitting, we reached that same 300-micron level in less than one minute.
Most of the time you’re going to be evacuating a circuit that’s larger and more complicated than a simple cylinder. So the total evacuation time is going to be longer; nevertheless, you can use these percentages as a guide. It’s clear that if you’re evacuating through Schrader valves in your facility you’re losing a lot of time.
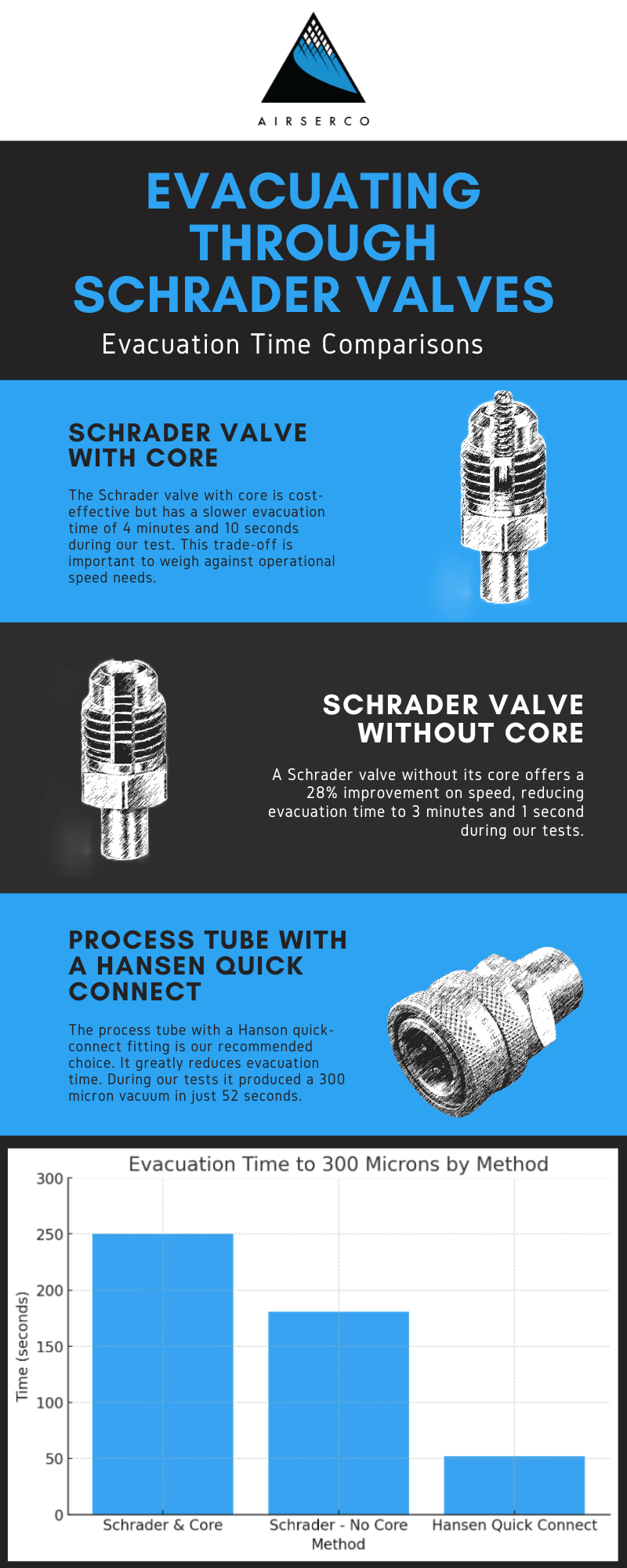
Time Is Money
Lost time can equate to lost floor space due to evacuating multiple units at once. You might need more pumps operating or more operators and probably, worst of all, may be missing important production deadlines. A lot of our customers will choose Schrader valves intending to save money or hassle in the short term or because they fear that adding a process tube might create another potential leak point or risk.
However, modern ultrasonic tube sealers like our URV20, for example, all but eliminate that risk and the process takes about a second. Time is money. So if it takes up to four times longer to evacuate through a Schrader valve, how much money are you leaving on the table?
As we saw during our tests, evacuation using a process tube with the Hanson quick-connect fitting is our recommended process. We recommend having a dedicated vacuum evacuation tube over 1/4″, ideally 1/2″ or 5/8″ to But sometimes during evacuation, we run into small leaks in our evacuation system. These small vacuum leaks can greatly add to the time it takes to pull a successful vacuum. Using temporary vacuum sealants like LuquiVac 4036 can greatly improve evacuation time no matter the connection you have. Sealants like this work well because they dry quickly, they are safe to use in evacuating refrigerant lines, they are resistant to most solvents, and they can be easily removed when the job is done. For more evacuation tips, read our article on HVAC and Refrigeration Circuit Evacuation Best Practices. Understanding methods for vacuum leak detection such as water injection, helium mass spectrometry, and untrasonic leak detection can prove very beneficial to understanding where the leaks occur.
More Questions?
Do you have an HVAC/R production problem that you’re struggling with or are you in the process of switching to flammable refrigerants this year? Feel free to reach out to us. With years of industry knowledge, we would be happy to answer questions you may have.
Shop Our Selection of HVAC/R Equipment
Looking to improve your performance or upgrade equipment? Browse our selection of manufacturing products to streamline your process and improve your performance.