Table of Contents
Oxy-Acetylene vs Oxyhydrogen Brazing
Most of us are still using outdated 19th and 20th century brazing technology, blissfully unaware that there is a much, much better way of doing things. We can hear some of you saying “If it ain’t broke, don’t fix it,” or perhaps, “We’ve been using oxy-acetylene for decades and people love our products.” However, we all know that we have to innovate in order to stay relevant, we must improve in order to remain competitive, and we cannot be left behind by competitors who update their production methods while we do not.
“we must improve in order to remain competitive.”
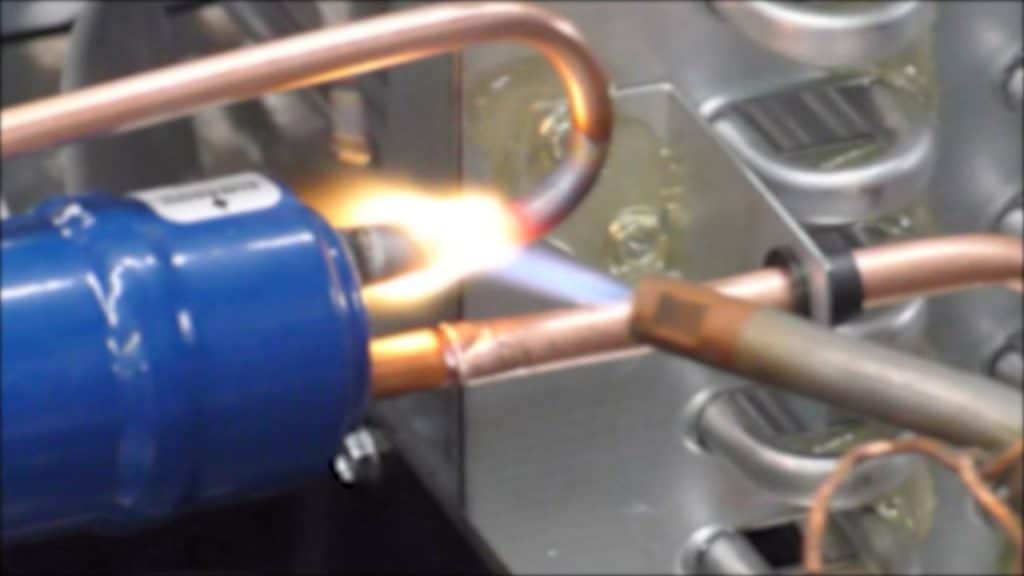
Why Make the Switch?
There are several problems with traditional brazing fuels. For example, what about all of that oxidation inside the pipe, contributing to early compressor and filter failure? Consider also the fact that every time your operator ignites their flame, they will dial in a slightly (or grossly!) different flame with a different temperature, providing extra variables for your quality team to sort through when troubleshooting production problems. Acetylene also produces a lot of soot that your employees breathe and that finds its way into your brazed joints.
These torches are also notorious for producing a wide, imprecise flame that sends heat in all directions – perfect for burning insulation, wires, aluminum and other expensive and time consuming repair items. They’re also needlessly slow, with low temperature flames that take forever to heat the joint. Finally, you’ve considered your gas costs, but what about the costs of gas transport, vendor management, floor space for all of those cylinders, and last but not least: the time and trouble that your technicians must dedicate to connecting and disconnecting manifolds, swapping and moving cylinders around the plant? Is your insurance charging you more for storing hundreds of cubic feet of explosive gases in your facility?
“There are several problems with traditional brazing fuels.“
These issues, some say, are simply the cost of doing business in our industry. However, it need not be this way. Airserco now offers an oxyhydrogen brazing system that industry leaders like Carrier, Daikin and others are now implementing in their factories worldwide. Using distilled water for fuel, it separates the two hydrogen atoms and one oxygen atom – a perfect fuel mixture, every single time. Your operators no longer waste time fiddling with dials and knobs to adjust the flame based upon how heavy their lunch was, how fast they want to wrap that last unit up, or any other reasons. As a result, the consistency of your production process improves.
I mentioned oxidation above, and while oxidation is simply a factor of heating your copper pipes, the oxyhydrogen system produces on average about half the oxidation inside the pipes. This is because oxyhydrogen combustion produces a 7,000 degree flame (compared to around 5,800°F (3,200°C) for oxy-acetylene… depending upon how your operators mix the flame – see previous paragraph). A hotter flame means less flame contact with the joint, and that means less time for heat transfer along the pipe. This reduced heat transfer is what reduces the oxidation.
“A hotter flame means less flame contact with the joint”
Airserco’s oxyhydrogen brazing system boasts several additional benefits, including:
- Improved pipe strength near brazed joints (heat will weaken your copper, so less heating time means less heat transfer and therefore reduced weakness in your pipe structure);
- The oxyhydrogen flame produces no CO, no C02, no soot and no fumes;
- This low-pressure system generally operates at less than 10psi, with all gas generated on demand from distilled water – no more cylinders and no explosive gas storage;
- Its extremely concentrated flame only produces heat where the flame is present. It is perfect for brazing in confined spaces, near insulation, wiring and other sensitive components;
- The benefit of significant cost savings compared with traditional fuels – only electricity and water are required!
Oxyhydrogen vs Oxy Acetylene Difference Table
Aspect | Oxyhydrogen Brazing | Oxy-Acetylene Brazing |
---|---|---|
Fuel Source | Distilled water (hydrogen and oxygen generated on demand) | Acetylene gas stored in cylinders |
Flame Temperature | Approximately 7,000°F (3,871°C) | Approximately 5,800°F (3,200°C) |
Flame Characteristics | Highly concentrated, precise, & consistent | Broader, less precise, and variable |
Oxidation Inside Pipes | Produces less oxidation due to shorter heating times | Higher oxidation due to longer heating durations |
Environmental Impact | No CO, CO₂, soot, or fumes | Produces CO, CO₂, and soot |
Safety | Low-pressure system, gas generated as needed, no explosive gas storage | High-pressure gas storage with risk of explosion |
Cost Efficiency | Only requires electricity and water, reducing overall costs | Costs include gas purchase, storage, and transportation |
Operational Simplicity | Automatic flame adjustment, no manual tweaking needed | Manual flame adjustment needed for each use |
Application in Confined Spaces | Ideal due to concentrated flame | Higher risk of damaging nearby components |
Oxyhydrogen Brazing is the Future
Oxyhydrogen Brazing – Brazing Automation for HVACR Manufacturing
Oxyhydrogen brazing is qualitatively and quantitatively better in every respect, so why haven’t you switched over yet? There is an up-front investment, but there is less to modifying your gas distribution infrastructure than you might think. Because the oxyhydrogen system uses low pressure, it is distributed in flexible clear PVC hose with an abrasion-resistant cover. This means it is simple, fast and inexpensive to install, compared to black pipe or other materials. The oxyhydrogen gas generator can sit in a corner of your facility with a single gas distribution line from the to your brazing stations. The low pressure also means that its performance and effectiveness do not fall off over long distances – these lines can be hundreds of yards long without performance problems.
If you are interested in seeing this system, please feel free to contact us at staycool@airserco.com. We may be able to arrange an on-site demonstration. We look forward to hearing from you!