One of the most important procedures in the manufacturing of HVAC and refrigeration units is the evacuation (or degassing) of circuits. This procedure can be a major bottleneck of the manufacturing process since refrigerant charging is typically much faster than evacuation. Ensure all moisture and unwanted molecules are successfully evacuated from the system and reduce evacuation time with these evacuation tips.
Table of Contents
Overview – Evacuating a Line
It’s important to understand how molecules exit the system as it is being degassed. Just because a vacuum pump is used in the system does not mean that the molecules are being vacuumed out like a household vacuum sucking up dust. The vacuum pumps lower the pressure in the system making water turn to vapor at room temperature inside the circuit. In fact, according the the ACCA, when a system is pulled down to 500 micros of mercury, water boils at -12°F.
While doing this, the vacuum pumps create a negative atmospheric pressure outside the circuit which causes the molecules bouncing around inside (in a crowded space) to escape the system moving into a lower pressure area in the pump (a less crowded space). The molecules must find their way out of the system while bouncing around. Any obstacles or angles in their way can make it harder to bounce out of the system as portrayed in this diagram:
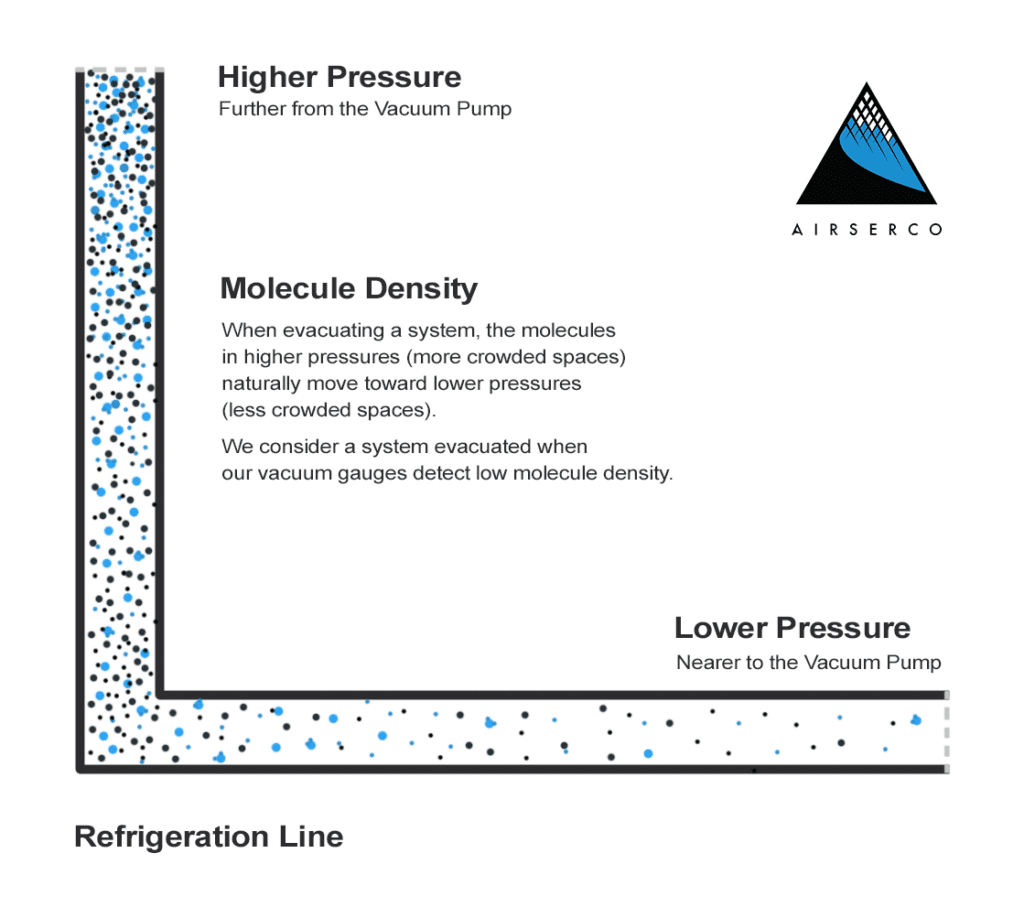
Evacuation Tips:
- Minimize the number of connections, orifices, valves, etc. between the vacuum pump and the circuit. These connections act as obstacles to the molecules that make it harder for them to find their way out.
- Minimize hose lengths and maximize hose diameters. Larger hoses allow more molecules to evacuate at the same time, and a shorter length allows them to evacuate faster.
- Reduce the use of elbows or sharp angles in the hoses. The easier the path for the molecules to escape, the quicker your evacuation times will be.
- Connect to high and low-pressure sides. Evacuating through connections from both the high and low sides of your circuit will allow the molecules inside your system to find their way out faster.
- Make sure your pumps are serviced regularly. Dirty pump oil can greatly reduce your evacuation performance because it will be unable to trap the moisture and other unwanted molecules coming out of your system.
- Make sure your system is sealed and not leaking. A leak in your system will work against your efforts to remove any moisture or air in the system. For this we recommend LiquiVac vacuum sealant for a temporary, high vacuum seal. Using high vacuum sealants can greatly reduce the time it takes to pull a vacuum.
- Maximize the inside diameter of any connections. Example: If you, are evacuating through Schrader valves, then you should remove the cores before evacuation. By removing the cores before you evacuate, you could save up to 25% of your total evacuation time. Replacing your Schrader valve setup entirely with a process tube and Hansen quick connect, we have seen 80% improvements in evacuation.
- Use an accurate vacuum gauge to ensure vacuum levels are correct.
If you would like to discuss your specific production line setup with our team, feel free to reach out.
Additional Tips:
Reassess Your Product’s Vacuum Requirements
One of the more effective and lowest cost ways to reduce your evacuation time is to really take a hard look at your vacuum requirements. I know, this isn’t a hardware change, but it really matters! If your current requirements call for vacuum down below 100 microns for instance, each additional micron can add a lot of time. So, get with your product engineers and really zero in on what your specific product evacuation requirements are. Sometimes you’ll hear “I don’t know, we’ve just always done it that way”, and there may be some room for dramatic improvement in your evacuation times simply by tailoring your requirements. If you’re at a loss, Airserco can help recommend some baselines as a starting point.
Evacuating Multiple Units Simultaneously
While the next option does not reduce the evacuation time overall, it does help with throughput. Try evacuating more units at once, so that the charging station has a steady supply of evacuated (or rough evacuated) units to keep it busy. Some highly efficient operations will have their units being evacuated on a roller or carousel as they move from one area of the plant to another so that when they reach the final evacuation and charging station, they can be processed in a minute or less. We offer both pre-vacuum (a.k.a. “rough vacuum”) stations as well as final evacuation stations which can perform rise/decay tests and record results, and even go straight to the charging phase in the case of our iRockall series, and these can even incorporate trace gas leak detection to combine several steps into one.
Vacuum Gauges – Why Accuracy Matters
When you properly evacuate a line you are ensuring absolute minimal levels of moisture and air – both of which are the main contributors to corrosion which in turn lead to system failures. Not only do you need to remove oxygen and water vapor for corrosion, but also non-condensable gasses found in air like nitrogen, oxygen, and argon.
As a result, when you remove the air and moisture from the lines, you avoid contaminant buildup in the lines over time, you help improve the lifespan of the unit, and you ensure optimal performance. This is why it is critical to have an accurate vacuum reading.
Installing a Fixed Vacuum Gauge in a Vacuum Pump Manifold
For industrial settings with custom built vacuum pump manifolds, we recommend precision built vacuum gauges that are fixed in place. We recommend installing these in the upper portion of the manifold, that way if any oil enters the line, the filament of the gauge is not damaged.
Precision Vacuum Gauges – Analog vs Digital
Analog vs digital? The choice is up to you. For engineers and technicians who are used to seeing a analog gauges, they may prefer analog. Many find it beneficial to physically see the needle moving down as the vacuum is pulled as this allows you to visualize the evacuation rate.
For others, it is nice to view the output like a digital clock – the precise numbers can be easily read from a distance by quickly glancing at the screen. For this reason, the digital gauge will provide more accurate readings if accuracy is paramount to your operations. Either way, these table-top vacuum gauges offer reliable performance, a simple interface, and precise measurements to meet specific needs in any laboratory or industrial setting.
How to Calibrate an Industrial Grade Vacuum Gauge
Because accuracy can be such a vital component to evacuation, it is sometimes necessary to recalibrate your gauge. One option is to purchase a calibration system that you can use in your own facility. The advantage to this is it allows your technicians and engineers to perform regular calibrations as necessary per your manufacturing requirements.
However, more often we see manufacturers will delegate the calibration to us at Airserco by sending us their gauge to have it professionally calibrated and promptly returned to them. This ensures proper calibration and it does not require the purchasing of additional calibration equipment.
For calibration inquiries or general evacuation questions, feel free to contact us for more information: